3D printing revolutionises the manufacture of sophisticated orthopedic implants
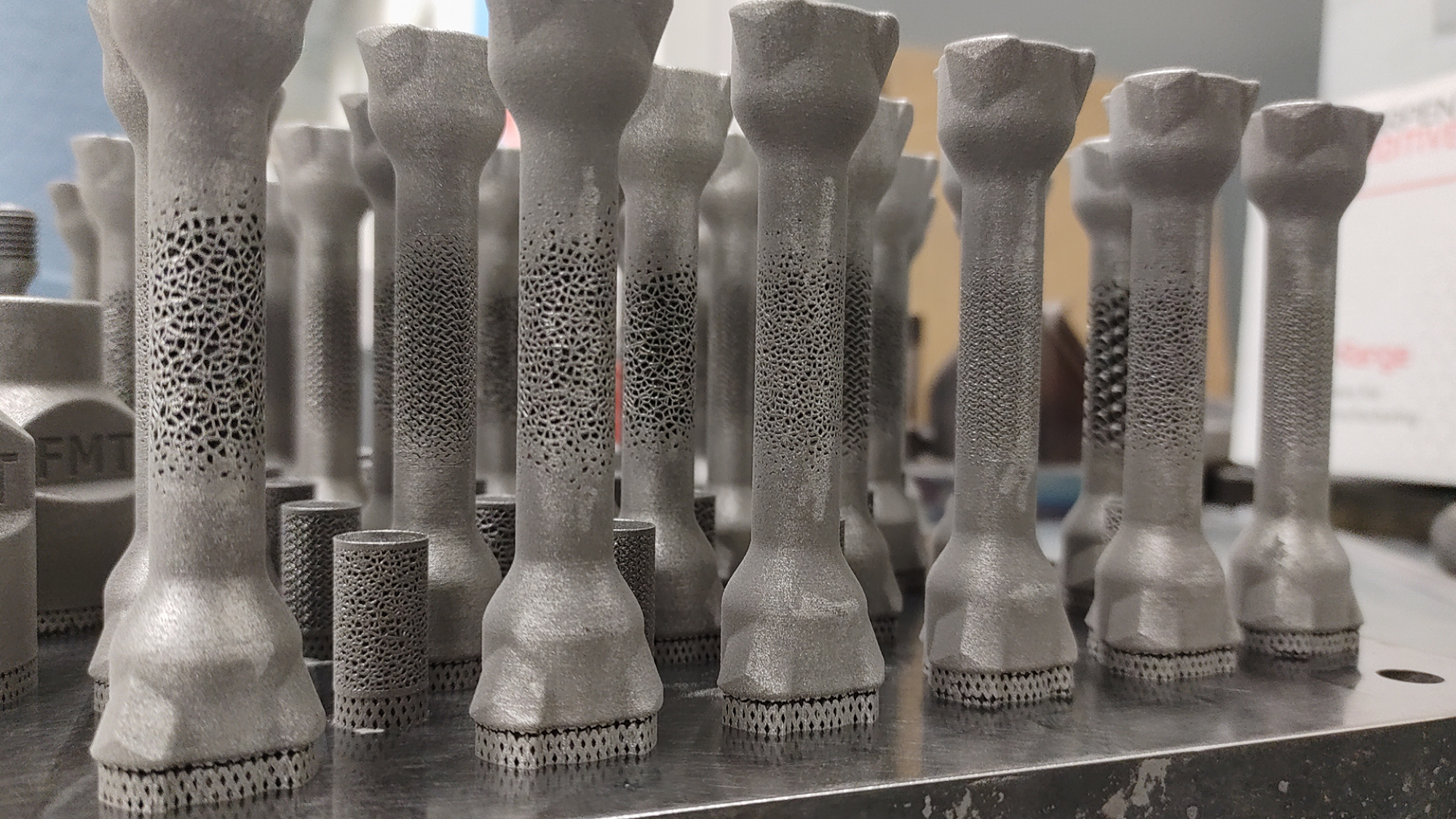
3D printing offers a fast process for the manufacture of custom-made implants. Its manufacturing precision and almost free geometric control provide a completely new paradigm for the development of implants. By exploiting the good features of the manufacturing process, it can address the shortcomings of traditional implants in terms of both mechanical properties and biocompatibility. 3D printing enables the development of complex structures that other manufacturing methods cannot achieve, for example, lightweight and durable structures can be designed with the possibility of optimizing structural details at the microscopic scale.
"In orthopedic applications, the main technical challenge is the high stiffness of the metals in relation to the different bone types. In use, a conventional rigid metal implant localizes the deformation on the surrounding bone tissue and can lead to premature failure," says Antti Järvenpää, Research Director of the Kerttu Saalasti Institute at the University of Oulu's Future Manufacturing Technologies (FMT) research group.
In a collaborative study, the Future Manufacturing Technologies (FMT) group at the University of Oulu and the Costa Rican Institute of Technology have shown that by 3D printing purpose-designed pore structures instead of solid structures, the structural stiffness of implants can be optimised to meet the stiffness of different bone types. In addition, porosity can be controlled so that the implant surface can be made partially solid for durability but partially porous to enhance osseointegration and tailor the stiffness. The new type of implant takes advantage of these features so that it can be attached to the bone without screws. In this case, the bone tissue grows into the implant within the porous areas. The highly porous inner structure of the implant provides an excellent platform for the growth of blood vessels and nerve tissue.
The developed architectured materials can significantly reduce stress damage at the bone-implant interface and prolong the life of the implant. The structures developed can be used in the most common orthopedic applications, such as the hip, knee, or spine, but also in less common sites.
"The digitalised process, from CT imaging to customised implant manufacturing, enables surgical planning on a customer-specific basis. Developing customised implants allows for better coupling and adjustment between bone and implant. This can reduce the time, cost, and risk of surgical procedures. As a digital manufacturing technique, 3D printing has accelerated the implant manufacturing process and improved the quality of the products," says researcher Miguel Araya Calvo of the Costa Rican Institute of Technology.
3D printing allows for the shortening of the production chain as the rough and porous surface, often essential for biocompatibility, no longer needs to be produced separately by subsequent surface treatments.
Fatigue tests of metallic lattice structures have been carried out at the University of Oulu and at the Costa Rica Institute of Technology on a laboratory scale according to medical standards with promising results. Pre-clinical trials start in February in Costa Rica when researchers from the University of Oulu's FMT group traveled to Costa Rica with 3D-printed metal samples. The metal samples will be mounted on animal bones for mechanical laboratory testing and biocompatibility tests.
Future Manufacturing Technologies (FMT)