Materials and Mechanical Engineering
Materials and Mechanical Engineering includes four separate fields of study: Automotive and Work Machinery Engineering, Machine Design, Materials Engineering and Production Engineering. The research is also focused on four different focus areas, but with the common factor being the new high-strength steels and their manufacture, use and utilization in machines, vehicles and various structural solutions.
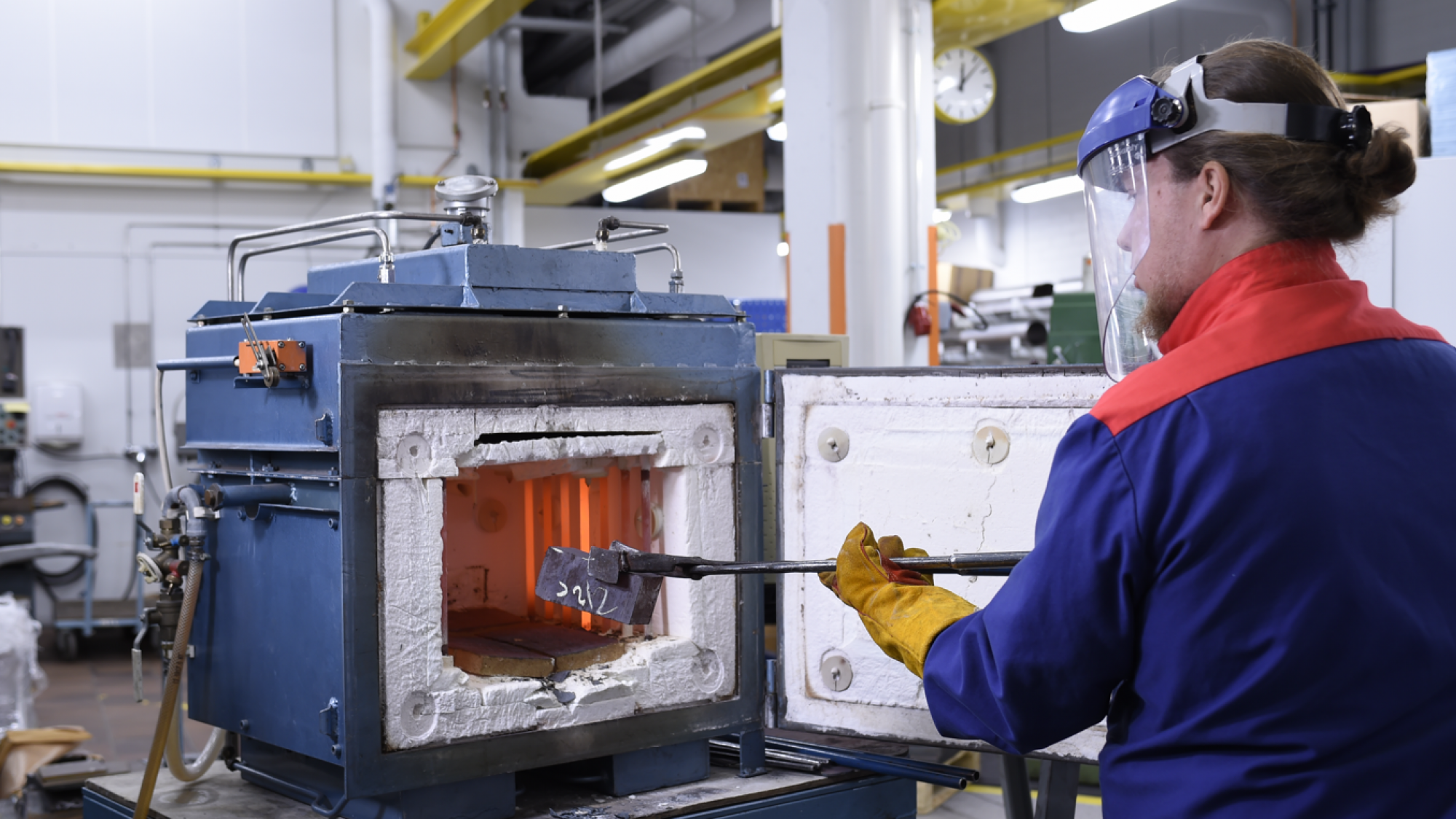
Materials Engineering educates experts for the needs of metal industry as well as the metal products- and electronics industries. Graduate engineers in Production Engineering play a key role in the design, control and operation of production lines in various industries. The study field of Machine Design delves into e.g. machine design, product development and machine construction technology. In Automotive and Work Machinery Engineering, the emphasis is on the design, product development and construction technology of heavy transport equipment and various modern work machines. Extensive training in all of these fields of study enables a wide variety of work assignments.
The research is directed to four focus areas, but with the common factor being the new high-strength steels and their manufacturing, use and utilization in machines, vehicles and various structural applications. Materials and Mechanical Engineering is the core unit of the Centre for Advanced Steels Research (CASR) at the University of Oulu and its research deals with the university’s strategic research area “Creating sustainability through materials and systems".
Facilities and machine shop.
Research groups
Projects
The email addresses of the staff are of form firstname.lastname@oulu.fi.
For staff phone numbers see phone book.